Check out this blog on barcodes and automated DTG.
First published in Images Magazine – Feb 18: https://www.images-magazine.com
The digital garment printing market has rapidly expanded over the last five years and continues to be a high growth area in the UK. In fact, the UK has now become a leader within Europe for digital print output in the garment sector. Our largest client has increased its number of Kornit Avalanche 1000 printers to 16 machines, and many of our other customers are continuing to expand as well.
It is well reported and generally understood that system maintenance and environmental conditions are important factors for a successful digital garment printing facility, but the importance of workflow is often overlooked.
Automated workflow
The majority of digital garment print output is based on short run, multicolour print work and a high percentage of this work is based on e-commerce retail and e-commerce fulfilment. This often means that average run lengths are as low as one or two pieces, with each job having a different garment, colour and graphic file. The production requirements for any single customer are growing rapidly and figures of over 1,000 such jobs a day are becoming more common.
Many digital print shops start with a manual workflow system that involves printing out an order form, picking the garment from warehouse stock and sending in piles to the print department. The file is then manually opened from the relevant storage folder and sent to print. This is labour-intensive and time-consuming to the point where this manual system restricts the production output on some of today’s high production printing machines.
There is nothing wrong in starting off with a manual workflow such as this, but it is best to avoid becoming stuck in the rut of ‘don’t change it when it is working’, especially when your business is expanding.
To achieve the throughput expectations on Kornit high production industrial DTG printers, it is often necessary to automate the workflow and reduce the labour and time constraints for each print job from receipt though to picking, pretreatment, print, dry, pack and dispatch.
There are several suppliers, such as Custom Gateway, that are active in providing automated workflow systems that specialise in affordable automation and control of the print throughput. These systems enable files to be processed automatically from orders placed online and downloaded to a hot folder with coding that matches the print output system. With Kornit printers, this coding includes the pre-treatment level, colour management, preview, job description, print size, position and quantity.
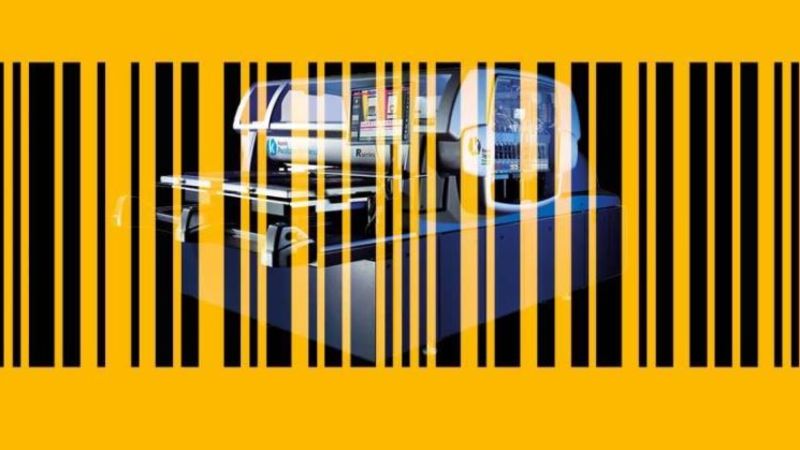
Barcode reading
Increasing production throughput means that the garment picking area can also become labour intensive and a bottleneck waiting to happen. The automation of workflow should include linking to barcodes, where a barcode is produced for each job with all the aforementioned coding parameters linked to it. The barcode can then be printed on a label and attached to the garment at the picking stage.
Once the bulk orders arrive at the print department, the barcode is read at the machine and the graphic preview with all print parameters is pulled from the hot folder and entered into the print queue on the machine. Automated feedback from the reading of the barcode can be sent to the client to confirm that their order is being printed.
The barcode can remain on the garment throughout the drying and packing process, providing ‘print complete’ and dispatch notices to the customer when read at each stage.
I have seen various automated workflow systems that operate with some honed areas that suit individual requirements for workload, throughput, garment and job variants. One aspect that often changes is the way the jobs are handled after the print and dry process is complete. Some will dispatch straight from the end of the dryer and others will stack garments after drying in job batches. This way, orders that have multiple garment types can be gathered in a final job completion area and dispatched together as one order.
In addition to job workflow, these automated systems will also handle stock re-ordering and enable remote access to follow and manage order intake, progress and completion to provide total control over your production even when you are away.
When deciding to operate an automated workflow system there is always involvement required to ensure the system operates according to your specific needs, whether you have opted for a bespoke system or a more generic one. It is undoubtedly worth the effort in the long run, as the rewards from efficiency and resulting reduction in unit costs are significant.
Recent articles
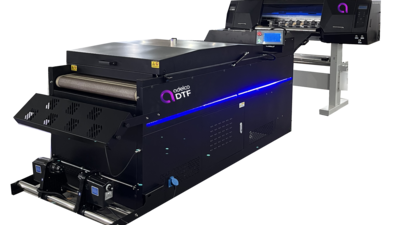
Why Precision Matters: The Role of Accurate Cutting in DTF Printing
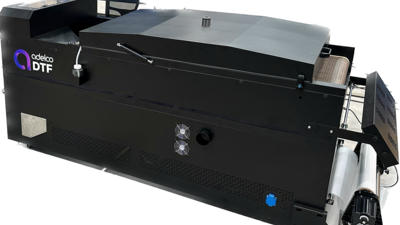
Eco-Friendly Printing: How Integrated DTF Systems Reduce Waste
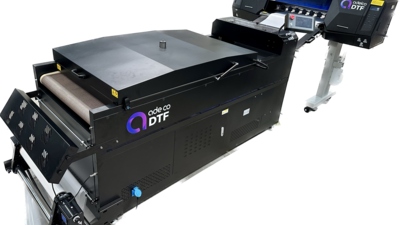